Imagopack
Processing industry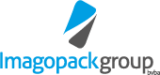
Imagopack enjoying growth thanks to the LISA ERP application opening up new perspectives
Achieving a 25% increase in turnover with the same workforce: this is Imagopack’s target for the next three years. Thanks to the implementation of “LISA”, the ERP application from Claerhout Computer Engineering, the packaging and spices distributor has succeeded in optimising its operation to such an extent that this growth objective is indeed achievable.
Imagopack originated from Imagopak, a packaging materials wholesaler that was taken over by Pascal Biebuyck and Vicky Damman in 2008. The couple had previously been active in mushroom cultivation, but they were looking for a new challenge with which they could further explore their knowledge and skills. “Packaging seemed like a great opportunity as it allowed us to target the sectors we feel we were most closely related to, namely the food industry and food retailers,” says Pascal Biebuyck. “We moved the company to larger premises in Desselgem where the ball started rolling quickly. In 2011, we also took over Merelbeke-based company, Josy Verpakkingen. And two years later we decided to include Mareco in our portfolio as well. This herbs wholesaler allowed us to offer a wider range to our customers, the food companies and butchers.”
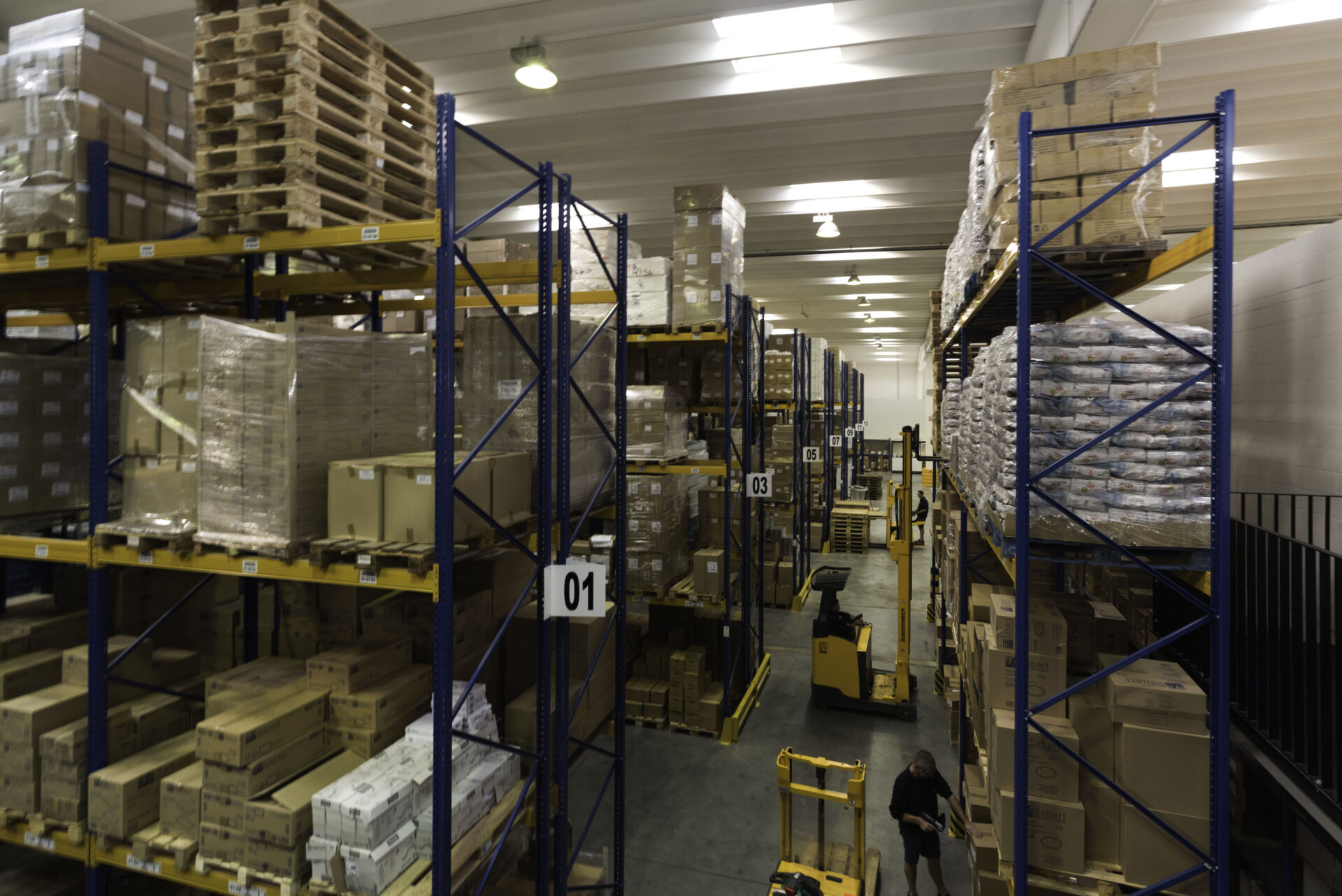
Process optimisation necessary
Because the existing base could not accommodate the three companies, the managers decided to invest in a brand new building. They found a suitable piece of land for this purpose on the Deerlijk industrial estate, where they started at the end of 2014. “It was a period in which we wanted to dot the i’s and cross the t’s,” says Pascal Biebuyck. “For example, at the end of 2013, we integrated the three companies into the Imagopackgroup. In the meantime, we had taken a close look at our processes and came to the conclusion that we absolutely needed complete warehouse management with RF terminals. In our former location, the information was kept the minds of our employees, with all the problems associated if they were absent from work. So pallets were often placed in the wrong place, an employee would not know where he had stored what, or he would forget to order additional packaging, resulting in stock shortages. We also had no idea what we had in stock, let alone what the rotation time of all the products was. Finally, incorrect deliveries could not be ruled out and we were not always able to respond to orders quickly. In short: these circumstances are not particularly positive if you have the ambition to grow strongly.”
Existing ERP application does not help
Such problems are obvious if you don't have an ERP package. But Imagopack had worked with an ERP application for years. “Unfortunately, the solution was not able to keep up with our growth,” says Pascal Biebuyck. “This was mainly due to the lack of full integration. Certain modules came from other suppliers, so communication sometimes went wrong. And if something was wrong, everyone pointed the finger at others. The second problem: we wanted to introduce RF terminals for inventory management. But this required a thorough reprogramming of the ERP application. Finally, we were not really happy with the relationship we had with our ERP supplier at the time. Not only did we feel like a ‘number’. Agreements were not kept; we had to wait a long time to resolve breakdowns; we received higher invoices than anticipated, etc. In short: this was not a situation we wanted to take to our new location. Although we had already invested a considerable amount of money into the application, we finally decided in 2014 to start our ERP completely from scratch.”
LISA is an indispensable tool for companies with growth ambitions.
Choice for LISA
To ensure Imagopack would not go through the same difficulties, they decided to commit the necessary time to thoroughly research the range of ERP applications. “In addition to carrying research on the internet, we listened to our customers,” says the Imagopackgroup project leader, Pieter De Gheest. “We not only heard the name LISA regularly, but it was always associated with very positive stories. The fact that one of our customers had been using it for about ten years without any problems and had enjoyed enormous growth was the deciding factor for us to request a demo. Although we were already convinced, we still gave three other players the same chance. But no other application could match ‘LISA’ in terms of user-friendliness, completeness, potential to evolve with the company and, above all, alignment with our activities. After all, this ERP application is fully geared to the food industry, which is ideal for us. On the one hand, all our customers are located in this sector. On the other hand, we are part of the same sector, since we fill our spice mixes and sauces here ourselves.”
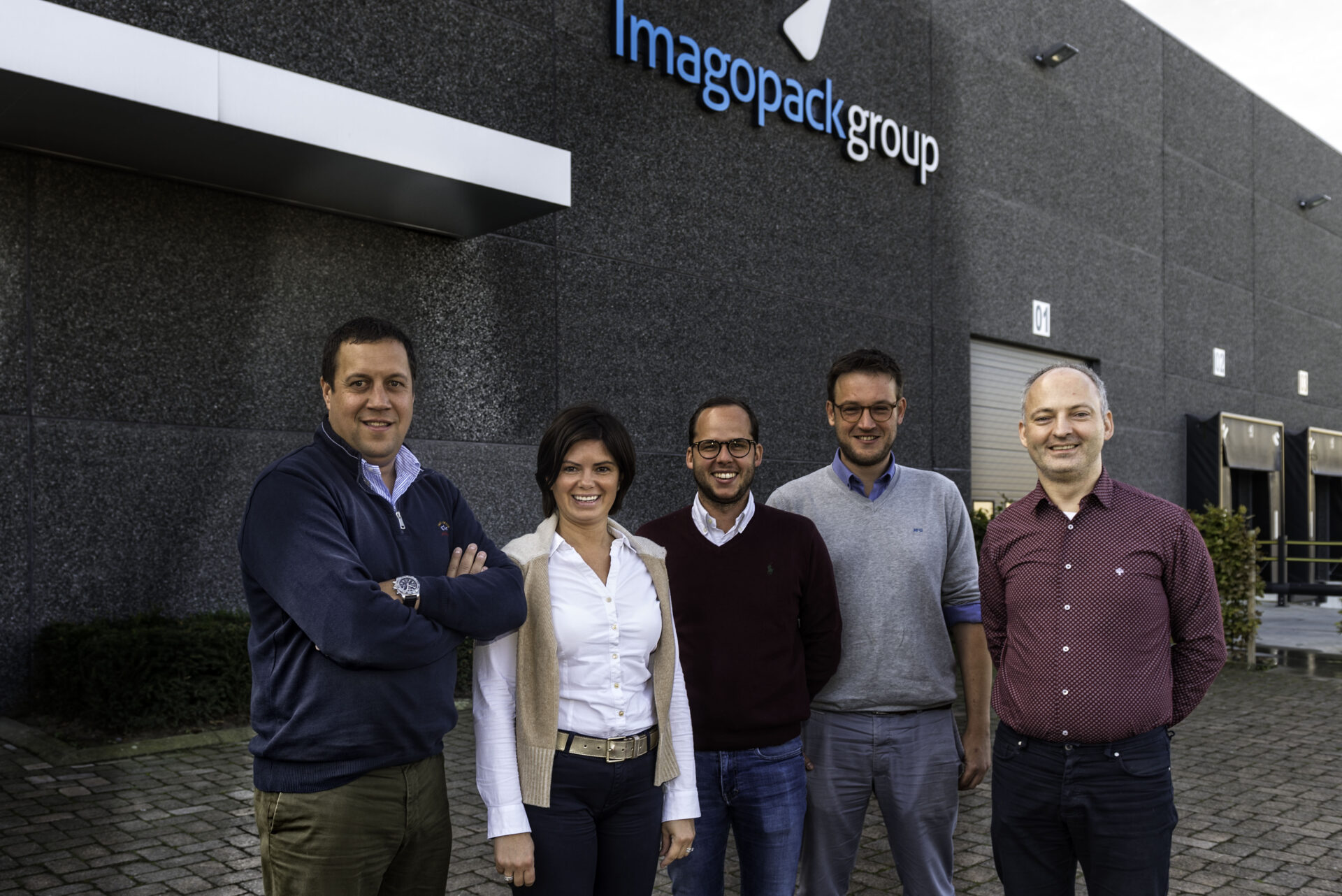
CCE MAKES THE DIFFERENCE
However, it was not only the capabilities of ‘LISA’ that were decisive. The Claerhout Computer Engineering (CCE) developer/implementer was also, and maybe even especially, very popular. “They are a real family business and manager Geert is committed to his staff, which is reflected in a team that will do anything to satisfy the customer,” says Pascal Biebuyck. “Since we have the same philosophy, we immediately felt at home. CCE also strives for a real partnership with LISA users. You are not a number, and everyone involved is treated with the same respect. If an intervention has to take place early in the morning or at the weekend, it’s no problem at all. CCE has always been very quick to help us out. But what I personally thought was fantastic is that the consultants are worthy of their title. LISA is flexible enough to be tailored to your procedures rather than the other way around. Nevertheless, we consciously chose to adapt our way of working to the ERP package. After all, the CCE employees had shown us during the initial phase what optimisations and new possibilities this would lead to, and we are very happy we followed their advice. Although we have only been using ‘LISA’ for one year now, we have already made significant progress in all areas.”
Turnkey service
In order to avoid integration problems, and to make the most of the potential of “LISA”, Imagopack opted for the complete version of the ERP package, including the purchase and sales, invoicing, tracking, stock management, production and accounting modules. “The representative module, an application that offers tools to the representative to perform his job optimally, was also implemented from day one. Because we do not offer extensive row optimisation ourselves, and Imagopack needs this functionality, we built an interface with an ‘external’ application. CCE itself has taken responsibility for integrating both packages to ensure communication problems never arise,” says Dieter Rutten, ERP project leader at CCE. “Our customer was very afraid of encountering the same difficulties as before. This is because they opted to purchase all the required hardware from us as well: servers, wireless Wi-Fi, scanners, tablets for the sellers, etc. Precisely the fact that we can provide a “turnkey” solution if necessary is surely a CCE asset appreciated by many companies, not least by Imagopack.”
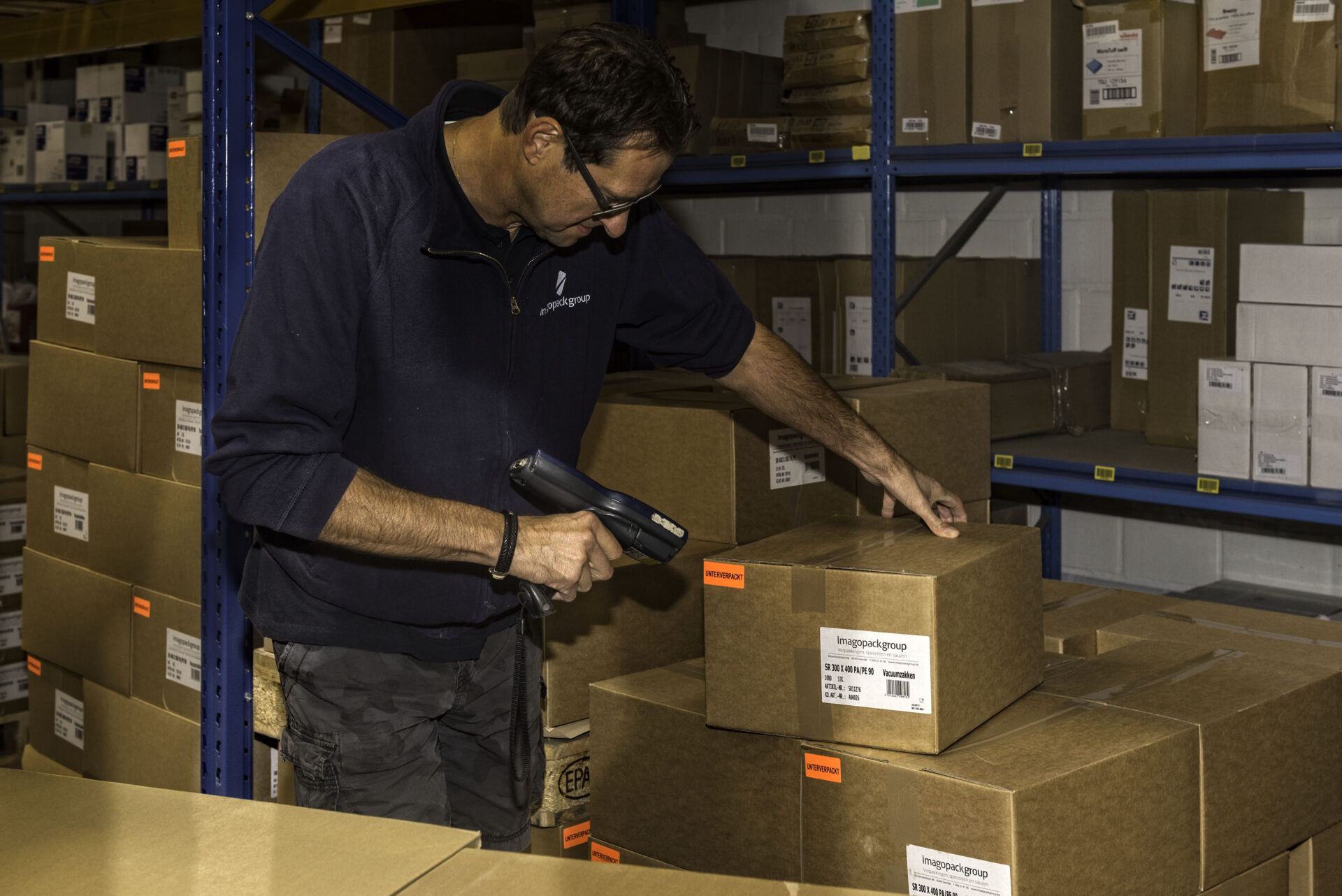
Start from scratch
In order to achieve an easy start-up and operation, Imagopack chose, on the advice of CCE, to start completely from scratch. In other words: data from the previous ERP application was not used. All the data was re-entered afresh. Pieter De Gheest: “This meant we didn’t put incorrect information into ‘LISA’. In addition, it was a good exercise for us to verify and adjust all the data. Of course this entailed a lot of work. And it even ensured the full start-up of ‘LISA’ occurred a few months later than planned. But the big advantage was that there were very few teething problems and we can now rely on both the application and the data 100%.”
An indispensable tool
Although the implementation of a new ERP package required considerable effort, Imagopack does not regret its choice for a minute. “Thanks to ‘LISA’ we have made rapid progress,” says Pascal Biebuyck. “The error rate in terms of orders, deliveries and storage has been reduced to almost zero. The package has also proven itself capable of responding perfectly to changes; we took over Beelprez Packaging from Marke at the end of last year and integrated their activities into the group without any problems. In 2018, we also want to double our capacity of 3,000 pallets by building a new warehouse. And we are 100% sure ‘LISA’ will cope with this change without any problems. It is striking to see all our processes running much faster and more efficiently. Transparency is now a thing as well, which has brought enormous peace of mind to the company. In short: the ERP package provides us with the ideal basis to achieve our objectives. After all, by 2020 we want to grow our turnover by 25% without having to recruit extra manpower. ‘LISA’ optimises the operations in our company and offers us the opportunity to further expand our range and to optimise stock. We can therefore say that this ERP application is an indispensable tool for companies with growth ambitions.”
Pictures Marc Masschelein