Fribona – “In its standard form, LISA offered all the functionality we needed”
LISA AT FRIBONA
Fribona specialises in pre-cooked frozen meals. This company is located in Oostkamp. Omer Adriaens founded Fribona in 1960 on the Vrijdagmarkt [Friday Market] in Bruges. He initially started by selling frozen products to people’s homes. He was the first in Europe to do so. Gradually he started producing frozen meals and shifted the emphasis to social catering, i.e. B-2-B customers. In 1999, Fribona even stopped the home service completely. Focus shifted to industrial kitchens and food services. A few years later (2007), Marijke and Patricia, Omer’s two daughters, took the helm of the company. Today, the third generation, Thomas and his brother Laurens, are also working at Fribona. In recent years, the health card has been focused on their own production. Thomas: “Nowadays, more than ever, hospitals want to offer healthy food whenever they want. Fribona offers ready-made answers. The meals we currently produce contain less fat, less sugar, etc. And we are also offering more and more vegetarian dishes.
Fribona certainly didn’t choose the easiest path when they started looking for the best ERP package for their food company. Three of the ten candidates survived the initial selection round. These 3 candidates were presented with some challenging scenarios and told to demonstrate their solutions during the final round. The conclusion was obvious: It was soon obvious that LISA from Claerhout Computer Engineering was the best choice for Fribona.
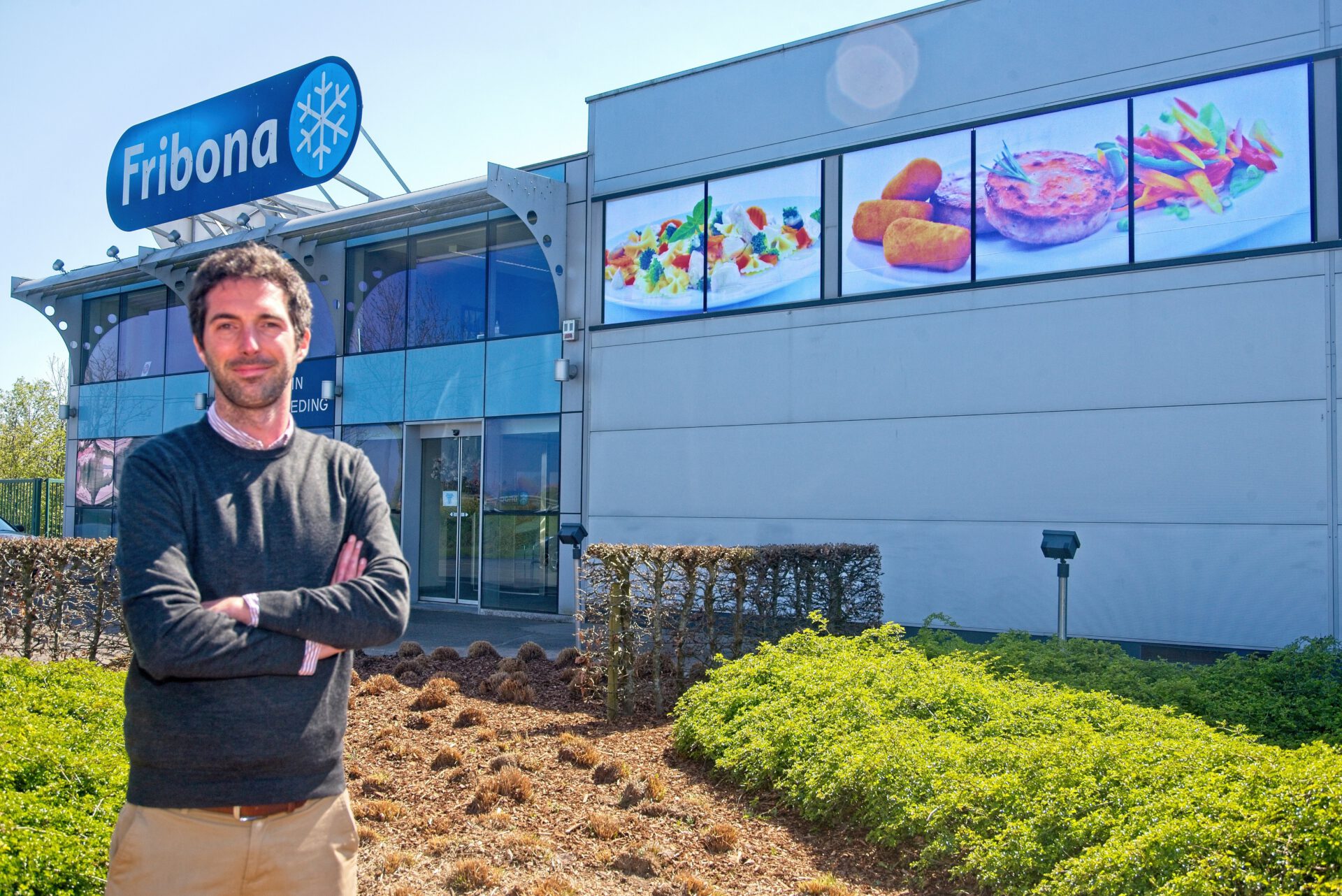
Thomas Theys, grandson of the Fribona founder, was appointed to lead Fribona into the new digital era 3 years ago. With previous professional experience, he was ready to face the challenge. “Fribona specialises in producing ready-to-eat foods that are pre-cooked, sliced or otherwise add value to social catering (education, hospitals and company restaurants). The Fribona range covers an entire menu and varies from appetisers to desserts. Some examples include paella, vol-au-vent, stew, soups, croquettes, hamburgers, roulades, etc. We then supplement this range with trade goods such as frozen vegetables and desserts,” says Thomas.
The range and production of Fribona is therefore very extensive. “We couldn’t go anywhere with the existing (strongly outdated) IT programme. With each expansion, we needed additional customisation. After applying customisation on top of customisation, our supplier was no longer able to help us any further. This forced us to look for a new ERP supplier that offered a standard package to do what we needed.”
We were looking for a standard ERP package, and found it in LISA, which met all our needs in its basic version. – Thomas Theys
EXTERNAL HELP
The search for an ERP package started with an internal study. “We analysed the players in the market with experience in the ERP food industry. We made a wishlist and decided to look for a programme with many functionalities from that list were already available in the standard package. We wrote to about ten partners. Each company presented their product in a demonstration, and after internal discussions, we filtered out three candidates.” “We then continued the selection process with an external IT consultant. Three more extensive demos followed, each of which were attended by a large number of our employees. In the end, CCE’s LISA came out on top.”
What was special about Fribona was that so many employees were involved in the choice of the package. Thomas: “Getting our employees involved so heavily cost us a lot of time and money, but we believed this was the best approach. We didn’t want to push anything from above. We introduced the employees to the package informally. After all, you can rightly assume you will have difficulties if your employees are not behind such a transformation. Most of the people working here have been with us for 20 years. They were already familiar with the previous package. A new ERP package would completely change their way of working. It was extremely important to us that the introduction of LISA would be widely supported. In the end, everyone was convinced that LISA was the best fit to meet all the predefined requirements.”
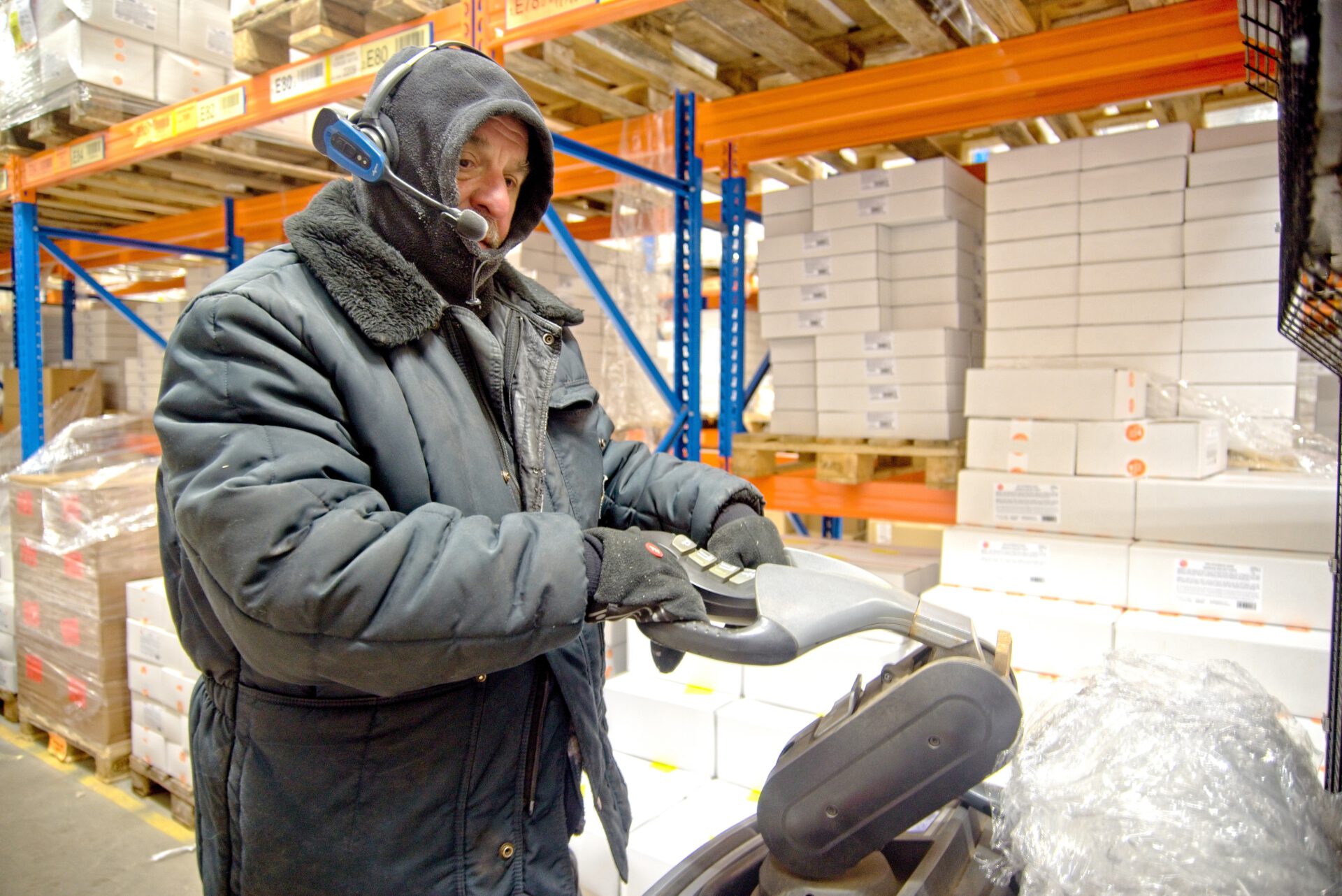
IMPLEMENTATION
Implementation of LISA started in February 2020. However, the corona pandemic threw a spanner in the works. As a result, everything had to be discussed remotely due to the lockdown. CCE normally prefers face-to-face contact with the end customer, but this had to be “remote”. Fribona finished collecting the master data and flows in August 2020. “In addition to the implementation of the standard flows in LISA, the integration with external systems posed a major challenge within the project. There was not only a VoicePicking system, but also a route optimisation programme, floor scales and a brand new webshop. In concrete terms, this meant four external parties had to go ‘live’ with LISA at the same time”, says CCE’s Dieter Rutten. “This makes planning a bit more complicated because you have to rely on the goodwill and commitment of external partners. We had already had positive experiences with most of the partners.”, he continues. “Fribona had asked us to start up all the modules at the beginning of 2021. In addition, CCE was also chosen to renew the entire server infrastructure, including firewall. A handful of challenges that needed to be overcome simultaneously on all fronts.”
The VoicePicking in the deep-freeze warehouse was flawlessly connected to LISA.
START UP
As agreed, LISA went “live” on 1 January 2021. “This is when, in accounting terms, the new financial year starts. But it’s a bit more difficult in terms of production because it is super busy at Fribona in December. This gave our employees less time to deal with the implementation of the new ERP programme,” explains Thomas. “Due to corona, it was a little less busy. For example, many visitor restaurants in hospitals or school restaurants were closed. We were able to make the best of a bad situation. It still required a lot of effort from all the employees involved, and we spent many hours on it, but we succeeded and get everyone their promised time off over the holiday season.” Dieter: “The VoicePicking started on 4 January 2021, with the first delivery scheduled for the following day. Everything went smoothly. A CCE employee remained at Fribona during the entire first week to offer support and guidance.” Thomas: “Everything was tested beforehand, but once you go ‘live’, you notice other scenarios. Fortunately, we had been able to start using various modules step by step in December. In the end, it all ran smoothly and unforeseen issues were resolved by CCE immediately, and they provided us with constant guidance through the Go Live process. The deadlines were met as agreed. After a few days, CCE was no longer required and things were buffered internally by the key users.”
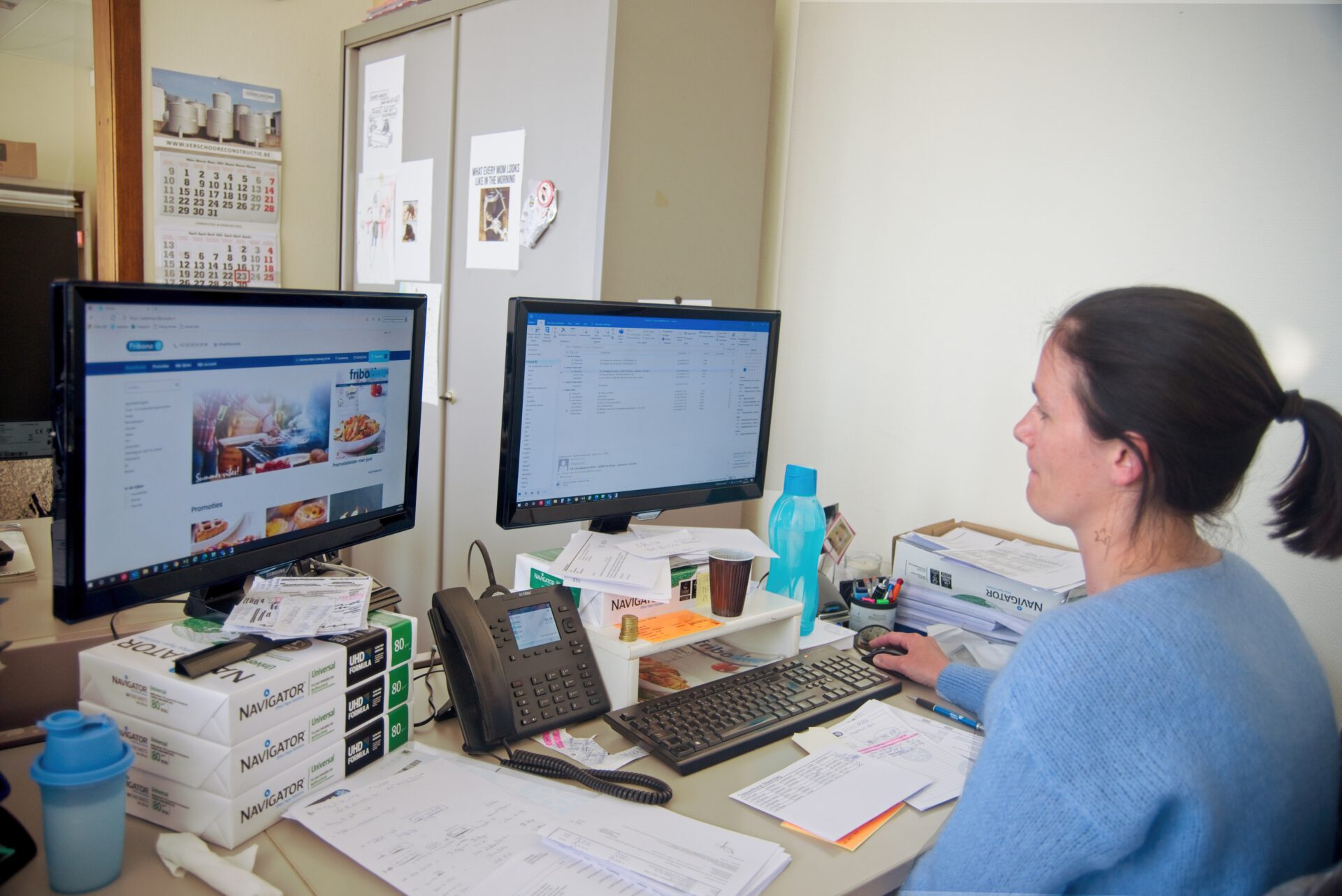
VALUE
Thomas: “Now we are a few months down the line, I can take a look at the process from a distance. Overall, I am super satisfied, because no customisation was involved. The basic version of LISA meets all our needs. I also love the digitised invoices. One push of a button and all the invoices are sent. How easy is that? No more paper and postage. This saves time and costs.” “I am just as satisfied with the order entry and the processes that follow, including VoicePicking, stock management, route calculation, administrative follow-up of order status, printing of delivery notes, etc. The whole process runs smoothly and is a lot more efficient than before. It allows us to manage things better after receiving the order. If we need to, we can change processes within LISA ourselves. For larger changes, we can always call on the team that looked after the implementation. Reporting has also improved. We want to link the reports to Microsoft Power BI in the future. And last but not least, the link to the BarTender label programme is an absolute dream. The labels can now be adapted flexibly to meet the needs of our customers really easily.”
LISA has meant a serious improvement for the administrative team because everything runs more efficiently and clearly.
FUTURE
Thomas: “Purchasing an ERP package means a multi-year partnership. There has to be a good click between both parties. It is essential that the company’s own corporate culture matches that of the supplier. We noticed we had the same vision from the start. Further expansion is therefore assured.” “In time, we intend to digitise production further. And this will involve some serious exercise.” The future of Fribona also looks bright; the company recently received approval to expand. Thomas: “This will allow us to double our surface area to 10,000 m2, resulting in more flexible and efficient production.”