Meubar
Autres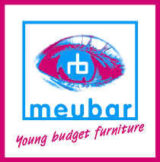
Le fabricant de meubles Meubar implémente une solution ERP et y couple un système de scannage de codes-barres.
Vendre des meubles abordables aux jeunes, voilà le point de départ de Meubar, un fabricant de meubles de Flandre occidentale. Une devise qui n’est pas évidente dans un marché qui doit se battre contre la concurrence acharnée de l’Europe de l’Est et de la Chine. Outre la recherche d’alternatives aux pièces de mobilier massif, l’automatisation et les codes-barres permettent également de répondre à la grande pression sur les prix. Fin 2003, Meubar implémentait le logiciel d’ERP LISA de Claerhout Computer Engineering (CCE) et y couplait son système d’identification automatique. Un an plus tard, la solution portait ses premiers fruits.

Meubar est actif depuis une cinquantaine d’années comme fabricant de meubles et possède une clientèle internationale. Mais l’entreprise continue à réaliser la moitié de son chiffre d’affaires sur le marché belge. Les références y sont des clients tels que Weba et Gaverzicht. Jusqu’il y a quelques années, Meubar proposait des meubles massifs classiques, mais en raison de la guerre des prix dans le secteur du meuble, l’entreprise est passée à la production de meubles en panneau aggloméré, qui conservent cependant le look massif. Une bonne décision, d’après Steven Verraes, administrateur délégué de Meubar.
S. Verraes : « L’Europe, mais aussi la Belgique, étaient réputées pour le mobilier en bois massif, mais ces dernières années ont vu des importations massives depuis l’Asie. » Ces pays ont non seulement l’avantage du coût de main-d’oeuvre, mais ils ne portent pas en compte non plus les matières premières, c’est-à-dire les arbres. La majorité des fabricants belges de meubles ont sombré face à cette concurrence. Le fait que ces meubles importés présentent beaucoup de fissures et de différences de couleur ne semble pas gêner le consommateur, alors qu’il ne l’accepterait pas dans un meuble belge. Nous essayons de réagir à la concurrence en copiant les meubles massifs en panneau aggloméré. Cela nous coûte la moitié du montant d'origine, ce qui nous permet d’afficher les mêmes prix que nos concurrents asiatiques. Mais la grande différence est que nous garantissons la qualité et le service. Nous livrons les réparations dans les deux semaines, alors qu’un conteneur met deux mois pour parvenir en Chine. »
Une autre approche
Le fabricant de meubles a connu une croissance continue au cours de ces dernières années et doit ainsi faire face à un manque de place important. Le délai entre la commande et la livraison atteint 4 mois, parce que le département d’emballage ne dispose pas de suffisamment de place. Meubar a déjà sous-traité 115 millions d'euros de production à des tiers afin de résoudre les problèmes de capacité. L’entrepôt ne peut plus accueillir lui non plus le volume de production accru, de sorte que les différents éléments de meubles sont actuellement stockés de-ci de-là dans l’usine. Il existe des plans d'extension, mais l’approbation du permis d’urbanisme se fait attendre. Heureusement, le nouveau système de codes-barres et ERP permet de garder le contrôle de l’ensemble.
S. Verraes : « Contrairement au passé, les meubles que nous produisons actuellement sont devenus des biens de consommation avec une longévité limitée. Nous sommes très sensibles aux tendances et devons donc lancer sans cesse de nouveaux modèles, ce qui a multiplié par 20 le nombre de références. Ajoutez-y le doublement de notre chiffre d’affaires en quelques années à peine, et vous comprenez que nous avons besoin d’espace supplémentaire. La philosophie de production a été modifiée elle aussi. Nous sommes passés du « make-to-stock » classique en grandes séries à une production avec un point de découplage. Les grandes plaques entrantes sont sciées en panneaux par des machines à commande automatique sur la base de la demande moyenne. Ces panneaux restent ensuite sur place dans un stock tampon jusqu’à ce que la production se poursuive sur la base des commandes clients. Un système qui fonctionne bien, étant donné que beaucoup de meubles sont composés des mêmes éléments. Cette procédure permet non seulement une plus grande flexibilité, mais également une réduction drastique du stock de produits finis. Nous continuons à affiner ce modèle en vue de maintenir le stock le plus générique possible au point de découplage, ce qui permet de réduire également le niveau de ce stock-là. Sur la base de la commande, nous parachevons les planches et emballons les produits finis. »
En raison du manque de place, chaque mètre carré libre est occupé par des produits finis. Un entreposage chaotique, qui est possible uniquement lorsqu’il est supporté par une application. S. Verraes : « Sans automatisation, cette croissance ne serait pas possible. L’étiquetage constitue également un point important, surtout parce que de nombreux produits différents sont emballés de la même façon et que les différences visuelles sont minimes. À mon avis, l’étiquetage exige encore trop d’énergie, mais c’est une nécessité. »
Automatisation flexible
La vitesse est importante pour travailler sur commande. Nous devons pouvoir changer rapidement de production et savoir si tous les composants sont disponibles et où ils se trouvent. L’ancien système de l’AGL Centaur était trop lent, ce qui a poussé Meubar à chercher une autre solution. S. Verraes : « La vitesse de réaction du système de Centaur était trop lente. Le calcul des besoins en matériaux pouvait prendre facilement toute une nuit. À chaque étape du processus de production, nous scannons les composants, ce qui revient en pratique à 5 millions de scans. Nous avions donc besoin d'une base de données capable de traiter rapidement toutes ces données. Progress nous a proposé la solution idéale. »
Le fabricant de meubles a posé deux exigences lors de la sélection du paquet : la solution devait comporter un configurateur de produit et un module de transport intégré.
La plupart des fournisseurs de logiciels proposent uniquement des modules de transport isolés. Nous recherchions un véritable paquet intégré, de sorte qu’il ne nécessitait pas d’interfaçage. CCE a pu nous en proposer un. Cette société a également écrit un morceau sur mesure, qui nous permet de décider à tout moment si nous allons acheter ou bien produire nous-mêmes. Le travail sur mesure sera proposé comme fonction standard lors d'une version ultérieure, ce qui nous offre un avantage lors des MAJ suivantes.
Au cours du projet d’implémentation, tant le hardware que les logiciels ont été remplacés. Il n’a pas posé de gros problèmes, et à chaque fois qu’il y avait un pépin, il était dû généralement à une erreur humaine. Tout le monde dans l’entreprise a été confronté au nouveau système, et il a donc fallu se familiariser quelque peu avec lui. S. Verraes : « Dans le nouveau système, tout le monde doit avoir la discipline de tout scanner ou saisir correctement dans l’ordinateur. Au début, de nombreux collaborateurs étaient très méfiants face à la nouvelle technologie, mais à l’heure actuelle, ils ne peuvent plus s’en passer. Nous recevons également de moins en moins de messages d’erreur parce que les collaborateurs ont adopté la routine pour travailler avec le système. Un autre avantage additionnel est la possibilité de remplacer nos collaborateurs. Dans le passé, lorsque quelqu’un était malade, nous avions un problème, parce que seule cette personne connaissait le département et avait par exemple élaboré un système de planification propre. Les différents départements étaient de véritables îlots. Nous avons mis fin à cet état de choses, car l’automatisation exige une intégration. »
La planification des besoins en matériaux (MRP) est automatisée, mais l’autorisation des commandes de production se fait manuellement. Il n’y a pas actuellement de planification à capacité finie, mais cela pourrait changer à l’avenir. La planification largement manuelle se justifie par des considérations de flexibilité. S. Verraes : « En général, nous produisons des séries en un délai de 8 semaines, mais lorsqu’il y a beaucoup de travail, nous réduisons les séries afin d’obtenir une rotation plus rapide. Nous voulons également décider nous-mêmes quelle série produire en premier lieu. Il arrive qu’un client déterminé reçoive la priorité sur la base de considérations commerciales. L’esprit commercial est un don que les systèmes ERP ne possèdent pas encore. »
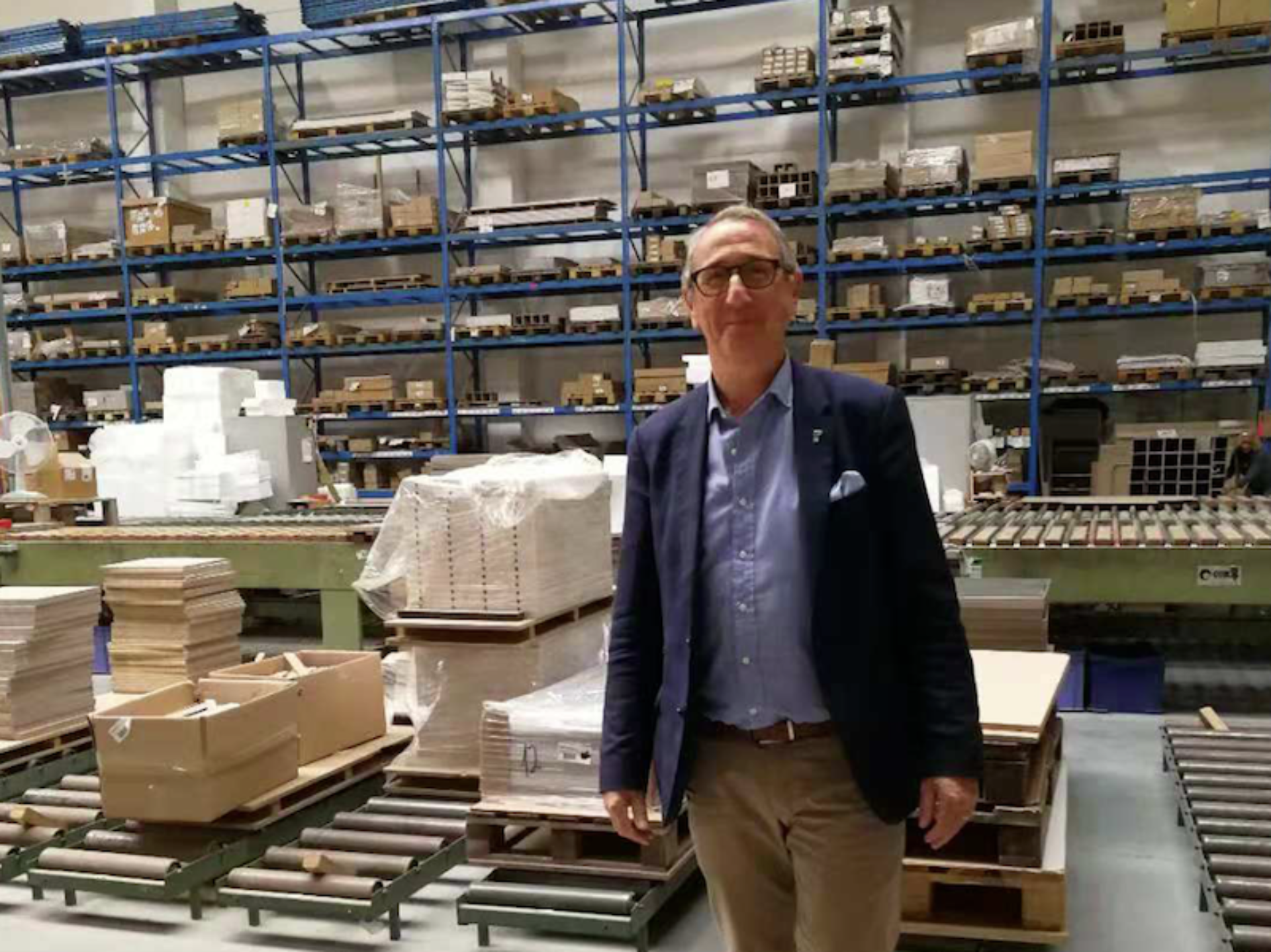
Le projet d'automatisation a démarré il y a 4 ans avec un investissement de 10 millions d’euros. L’accent était mis sur l’automatisation des machines dans la production, qui effectuent les configurations sans intervention humaine. Ce n’est qu’ensuite qu’on a envisagé des solutions logicielles. S. Verraes : « Dans le passé, nous n’étions pas partisans d'une automatisation. La flexibilité des solutions constitue un atout de taille, mais en cas de pépin, toute l’entreprise est à l’arrêt. Nous travaillons cependant avec un double switch et nos câbles sont posés en boucle, de sorte qu’il faudrait déjà deux ruptures pour que notre système tombe en panne. Il n’empêche. Plus l’activité était critique du point de vue service clientèle et fiabilité de livraison, plus elle a été automatisée en dernier lieu. »
L’entreprise a tout de même poursuivi l’automatisation, et est actuellement très satisfaite de ces choix. S. Verraes : « Pour la production de 1 000 armoires, nous arrivons en fin de compte à environ un surplus de 10 côtés et un manque de 100 fonds. On planifie en effet un peu plus d’armoires parce que des planches sont endommagées ci et là lors de la production. Mais il n’est pas possible de prévoir le nombre de ces dommages. Dans le passé, les défauts de fabrication n’étaient pas transmis automatiquement, ce qui entraînait des ruptures de stock. Aujourd’hui, nous connaissons toutes les données et le stock, et pouvons ainsi anticiper. »
Pour le flux entrant de marchandises, la fiabilité de livraison des fournisseurs est suivie au moyen de listes d’exception, qui comportent uniquement les livraisons tardives, incomplètes ou incorrectes. Le service après-vente profite lui aussi du système. S. Verraes : « Dans le passé, une seule personne effectuait toutes les réparations, mais dans le nouveau système, les retours sont traités comme des commandes normales. Un retour suit tout le trajet. Les retours figurent également dans la liste de chargement, de sorte que les collaborateurs qui chargent le camion n’oublient certainement pas le produit réparé. Pour nos clients, les réparations sont encore plus importantes que les commandes normales, et il faut en tenir compte. »
Trop petit pour une équipe IT propre
Meubar ne possède pas d’équipe informatique propre pour le suivi du projet ERP. Pour ce faire, elle fait appel aux services de CCE, qui veille à ce qu’un collaborateur IT soit présent deux jours par semaine chez le fabricant de meubles. S. Verraes : « Ce serait pratique de disposer en continu d'un expert en interne, mais une analyse coût-bénéfice nous apprend qu’il est plus intéressant pour une PME, du point de vue financier, de faire appel à un partenaire externe. En travaillant chaque jour avec le système ERP, nous découvrons quels rapports il serait intéressant de générer depuis la base de données, et comment améliorer les rapports existants. De nombreux progiciels de production proposent des rapports standardisés. Mais il est impossible d’éviter du travail sur mesure, car chaque entreprise de production suit une logique différente. »
Peut-on considérer qu’une implémentation ERP est achevée un jour ? L’activité change continuellement, donc également les processus de travail, et le progiciel doit suivre. S. Verraes : « L’implémentation est à peine terminée que vous envisagez déjà de nouvelles fonctionnalités. Ainsi, nous allons développer un site Web sur lequel nos clients pourront passer des commandes automatiquement. Cette procédure permet de réduire le nombre d'erreurs dans les commandes, et en outre, elle économise du temps. Il faudra cependant prévoir 6 mois pour la réalisation de notre site Web, parce que les listes de pièces des anciens produits doivent encore être converties. L’élaboration de listes de pièces correctes s’est révélée également la tâche la plus importante pour l’implémentation de notre ERP. La création d’un nouveau produit exige environ 2 jours de travail. Nous voulons également automatiser cette procédure d’une manière ou d’une autre, bien que ce ne sera pas chose aisée. Un ordinateur est un magnifique appareil pour effectuer des actions simples de façon répétitive, mais les procédures complexes uniques restent le point faible de toute automatisation.